焼結金属・粉末冶金・MIMの違いとは?

焼結金属、粉末冶金、MIM(Metal Injection Molding)は、いずれも金属粉末を原料とする加工技術ですが、その製法・対応材質・形状自由度・追加工の必要性などに大きな違いがあります。
本記事では、これら3つの技術の違いを明確に比較するとともに、製品開発・部品調達時における適切な選定ポイントを解説します。
また、ニアネットシェイプ品に対して必要となる追加工の重要性と、その課題を解決するための具体的な技術についても詳しくご紹介いたします。
焼結金属・粉末冶金・MIMとは?それぞれの加工技術の基礎知識
まず、焼結金属、粉末冶金、MIM(Metal Injection Molding)の3つの技術について、その基本的な製法と特徴を明確に解説します。これらはいずれも金属粉末を原料とする成形技術ですが、プロセスや用途、対応可能な形状・材質には明確な違いがあります。
焼結金属とは?
焼結金属とは、金属粉末を金型に充填・圧縮成形し、その後に高温で焼結することによって製造される部品や素材の総称です。この製造プロセスは、正確には「圧粉焼結」と呼ばれ、粉末冶金の中でも最も基本的かつ広く使用されている技術です。
なお、「焼結金属」という言葉は、完成した部品や素材を指す際に使われる名称であり、製造プロセスである「圧粉焼結」とは厳密には異なります。
たとえば、「焼結金属ギヤ」「焼結金属ブッシュ」といった言い回しは、部品名・材料名としての表現です。一方、「圧粉焼結によって製造されたギヤ部品」と言う場合は、その加工方法を説明する文脈となります。
このように、技術的な説明や文書においては「圧粉焼結」という用語を、製品やサービス紹介、Web検索対応の表現では「焼結金属」という用語を用いるのが一般的です。
焼結金属は、比較的シンプルな形状の中量~大量生産品に適しており、ギヤ、ブッシュ、軸受、スプロケットなどで広く使用されています。特に、切削加工では加工コストが高くなる複雑形状や硬質材に対して、材料歩留まりとコストパフォーマンスの面で優れた特性を発揮します。
粉末冶金とは?
粉末冶金は、金属粉末を利用して材料や製品を製造する一連の技術全体を指します。圧粉焼結やMIMもこの粉末冶金の一種に含まれます。粉末冶金は、金属粉末の配合、成形、焼結、そして必要に応じた二次加工(追加工)という工程で構成されます。
焼結と一体で扱われる場合もありますが、粉末冶金はより広範な技術領域で、含油軸受やフィルター部品、磁性材料、硬質合金なども含まれます。形状の自由度や材質の選定範囲において柔軟性が高く、用途によって専用の粉末設計が行われることも特徴です。
MIMとは?
MIM(Metal Injection Molding)は、金属粉末を樹脂バインダーと混合してペレット化し、射出成形機で成形した後、脱脂・焼結して最終製品とする粉末冶金技術です。プラスチック成形と類似したプロセスにより、非常に複雑かつ微細な形状を高精度かつ量産性高く成形できる点が最大の特徴です。
MIMは、医療用デバイス部品、時計部品、自動車の精密部品、電子機器の構造部品など、寸法精度と微細性が要求される部品に適しています。また、SUS系、チタン、インコネル、コバールといった難削材にも対応可能であり、焼結後の追加工によって機能精度をさらに高めることができます。
金属部品製造方法のまとめ
粉末冶金以外にも、金属部品の製造方法には、機械加工やプレス加工、鍛造加工、鋳造などもあります。まとめると下記のようになります。
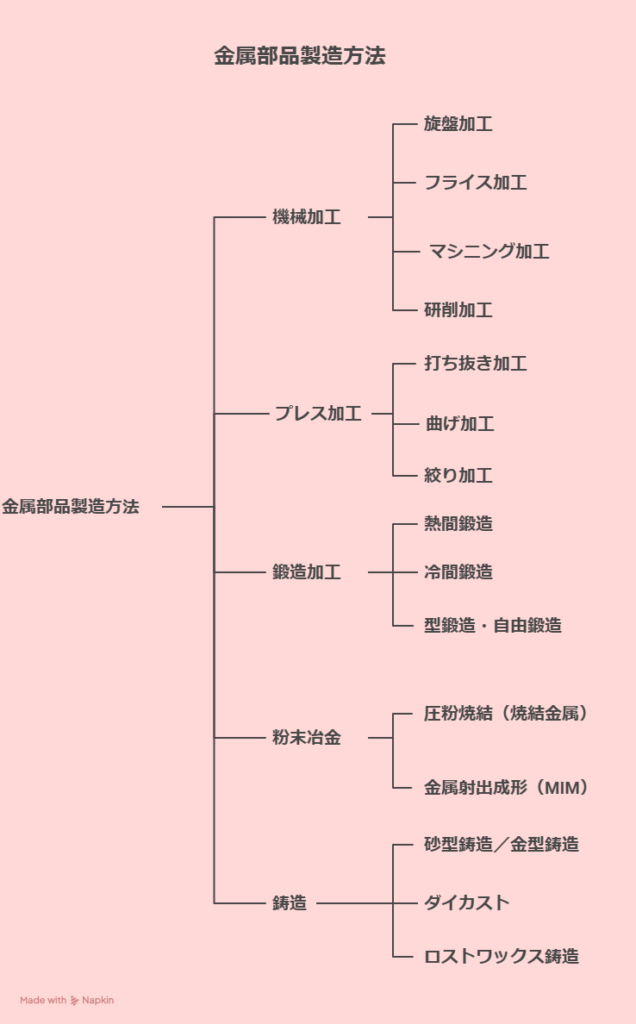
焼結金属・MIM・ロストワックスの違いを比較
焼結金属(圧粉焼結)、MIM(金属射出成形)は、いずれも金属粉末を原料とする成形技術ですが、成形方法、材質の選択肢、形状の自由度、精度、追加工の可否など、製品の要求仕様によって適した工法が異なります。またロストワックス鋳造も含めた3工法は、それぞれ異なる製造プロセスを持ちながらも、「中~小型の高精度部品を効率よく量産したい」という共通のニーズに応える代表的な工法です。ここでは、設計者や調達担当者が比較検討しやすいよう、主要な技術要素について表形式で整理します。
主な金属部品成形技術の比較
比較項目 | 焼結金属(圧粉焼結) | MIM(金属射出成形) | ロストワックス鋳造(精密鋳造) |
---|---|---|---|
成形方法 | 金属粉末を金型で圧縮後に焼結 | 金属粉末+バインダーを射出成形後に脱脂・焼結 | 蝋型で鋳型を形成し、溶融金属を鋳造 |
形状自由度 | △ 比較的単純形状向き | ◎ 微細・複雑形状に対応 | ◎ 複雑形状・空洞部品にも対応 |
寸法精度 | △ ±0.1~0.3mm程度 | ◎ ±0.01~0.05mm程度 | ○ ±0.05~0.1mm程度 |
対応材質 | 鉄系、銅系などが中心 | SUS、チタン、インコネル等も可 | ステンレス、アルミ、ニッケル等幅広く対応 |
ロット適性 | 中~大ロット向け | 小~中ロット(1,000個~) | 小ロット(10個~)対応可 |
追加工の必要性 | 穴あけ、研磨、ねじ加工等が必須 | 一部高精度部位で必要 | 一部寸法保証部位で追加工あり |
初期コスト | ◎ 金型費が比較的低く、材料歩留まりも高い | △ 脱脂炉・金型など初期投資大 | △ 工数が多く、型製作に手間がかかる |
主な用途 | ブッシュ、ギヤ、スプロケットなど | 医療・時計・電子機器など微細精密部品 | 航空機、医療用、芸術品など高付加価値品 |
どの工法を選択すべきかは、必要な精度・形状・材質・数量・コストなどによって大きく異なります。
たとえば…
- コストを抑えながらギヤや軸受などを中ロットで量産したい → 焼結金属(圧粉焼結)
- 微細で複雑なステンレス部品を量産したい → MIM
- 金型費を抑えて複雑形状の部品を少量作りたい → ロストワックス鋳造
といった具合に、製品設計段階での用途と特性に応じた適切な工法選定が重要です。
また、いずれの工法も追加工(2次加工)によって寸法・機能の最終仕上げが必要な場合が多く、特に「ニアネットシェイプ(ほぼ完成形)」に対する精密な穴あけ、溝加工、研磨などの技術力が、製品品質に直結します。
ニアネットシェイプへの成形後に求められる追加工とは?
焼結金属やMIMによって成形された金属部品は、いずれも「ニアネットシェイプ(Near Net Shape)」と呼ばれる、最終形状に近い状態で製造されます。これは、素材の無駄を最小限に抑えつつ、加工工程の省力化・効率化を目的とした製造技術ですが、最終的な部品精度や機能を確保するためには追加工(2次加工)が不可欠となるケースが多くあります。
なぜ焼結金属製品には追加工が必要なのか?
ニアネットシェイプ製品では、成形段階で一定の寸法公差は確保できるものの、以下のような理由から追加工が必要になります。
- 組付け部位の寸法公差を保証するため
⇒ 軸穴・嵌合部・ねじ部など、機能部位では数十ミクロン単位の精度が要求される - 滑りやすさ・気密性・回転精度などを向上させるため
⇒ 面粗度(Ra)や同軸度、平行度などの幾何公差管理が必要 - MIMや焼結品の成形特性によるばらつきを吸収するため
⇒ 成形焼結後に生じるわずかな収縮・変形への対応
このような背景から、焼結金属やMIMには、成形後の穴あけ、リーマ加工、溝加工、端面加工、研磨、ネジ加工といった仕上げ工程が求められます。
特に問題となる追加工の課題とは?
追加工においては、以下のような課題が現場で多く発生します。
- 成形後の焼結品は脆性があり、クラックや欠けが発生しやすい
- 小径・薄肉部への加工では、工具逃げやワーク保持が困難
- 追加工の工程が分かれると、段取り工数・リードタイムが増加
- 試作では高精度でも、量産移行時に同じ精度が再現できない
特に試作時には問題が出なくても、量産で精度がブレるというケースは非常に多く、設計段階から「加工を見越した製品仕様設計」と「量産性を見据えた工程設計」が求められます。
これらの課題を未然に防ぐためには、焼結やMIMなど成形技術だけでなく、その後の追加工を含めた一貫した加工技術を持つ外注先の選定が重要です。特に、
- ニアネット品に対する豊富な加工ノウハウ
- 専用治具や特殊工具の活用
- 高精度加工と品質保証体制の両立
- 試作から量産移行をスムーズに行える柔軟な生産体制
を兼ね備えたパートナー企業が、焼結金属やMIMの高精度部品を製作する際には必要不可欠となります。
焼結金属加工.COMが実現する追加工と高精度対応
焼結金属加工.COMを運営する株式会社宮本製作所では、焼結金属やMIMなど、ニアネットシェイプ成形品に対する高精度な追加工を得意としています。特に、設計者や購買担当者が抱える「試作と量産で精度が異なる」「異形状の加工ができない」「難削材が断られる」といった課題に対して、技術と体制の両面から明確な解決策を提供しています。
以下では、焼結金属加工.COMの差別化ポイントを6つに分けてご紹介します。
1. 成形金属への高精度追加工対応(ニアネットシェイプ形状品の仕上げ)
焼結金属やMIM成形品に対し、旋盤加工・マシニング・リーマ加工・研磨・ねじ加工などを行い、最終製品として求められる寸法精度や表面性状を確保します。複雑な形状や薄肉・小径部位にも対応可能で、「焼結で作れるが仕上げられない」といった現場の悩みに応えます。
2. 高同軸度・高真円度を実現する精密加工技術
自動車向けギヤ部品などに求められる高精度加工にも対応しております。高同軸度・高真円度の穴加工など、焼結金属品やMIM部品に対する付加価値の高い追加工を行うことで、最終製品の機能性・信頼性を担保しています。
3. コバール、SUS鋳物等の難削材への追加工対応力
特にMIMでは、SUS、チタン、コバール、インコネル、ハステロイ、パーメンジュールなどの難削材が使用されることがあります。宮本製作所では、これらの材質の加工依頼も数多く受けております。工具選定・加工条件・チャッキング技術まで含めて最適化した切削加工による追加工で、高品質な焼結金属製品を製作いたします。
4. 試作から量産まで精度を維持する専用ライン設計
試作で満足できる精度が出せても、量産で同じレベルを維持できないという問題は多くの現場で発生します。当社では、量産時にも同じ加工精度を維持できるよう、工程設計・治具製作・設備選定まで含めた専用ラインを構築することで、製品ごとの安定生産を可能としています。
5. 特殊工具の内製化による工程集約と短納期化
切削工程で使用する特殊工具について、当社では社内で設計・製作・再研磨できる体制を構築しています。1本の工具で4工程を処理できるなどの工夫を施した特殊工具で、大幅に工程数を削減しています。工具の最適化によって生産リードタイムを大幅短縮し、コスト削減と納期対応の両立を実現しています。
6. 開発部との連携による量産を見据えた設計支援体制
お客様の開発部門との技術的な連携体制も整備しており、製品設計段階から加工性・追加工性・量産性を考慮したVE/VA提案が可能です。「とりあえず試作したが、量産ができない」とならないように、お客様の製品開発から量産まで生産を止めないワンストップ対応を行っています。
加工品の事例紹介
続いて、実際に当社で製作した加工品の事例をご紹介いたします。
アルミ製 マニホールドブロック
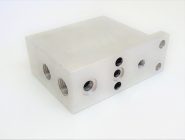
この製品は、アルミソリッド(ブロック)からの削り出しで加工を行った機械加工品です。加工方法としてマシニングにて6面加工を行っております。
段付き穴が非常に高精度な製品となっておりますが、専用の特殊工具を社内で内製化し、同軸度や穴径を確保しながらの加工を行っている製品となっております。
医療機器用マニホールドブロック
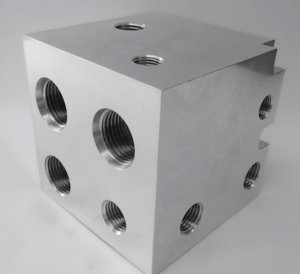
こちらは、医療機器の油圧システムに使用されるマニホールドブロックです。材質はアルミソリッド(ブロック)、サイズは80×80×80で、加工精度は同軸度・平行度・直角度を2/100に仕上げています。
マニホールドブロックで必要となる複数のポート穴は、ネジ部、シート面、座面などを多段で構成しており、油圧システムに接続するための厳しい精度要求に対応しています。また、4面に穴加工を施しており、そのうち1面にはサイズや形状が異なる4つのポートが設けられています。特に、穴の深さが最大70mmに及ぶ深穴加工については、当社オリジナルの自社製バニシングリーマを使用することで、精密な仕上げを実現しました。
産業機械用マニホールドブロック
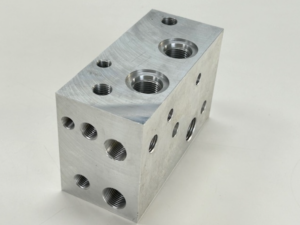
こちらは、産業機械の油圧システムに使用されるマニホールドブロックです。材質はアルミソリッド(ブロック)、サイズは120×80×50で、加工精度は同軸度・平行度・直角度を2/100に仕上げています。
本製品では、ネジ部、シート面、座面など多段構成の複数のポート穴を加工し、産業機械の厳しい精度要求に対応しています。6面に穴加工を施しており、そのうち2面にはサイズや形状が異なる3つのポートが設けられています。特に、最大75mmに及ぶ深穴加工については、当社独自の自社製バニシングリーマを使用し、精密かつ安定した仕上げを実現しました。また、長手方向の深穴加工にも専用工具を用いることで、高い精度を保ちながら対応しています。
焼結ギア(焼結歯車)
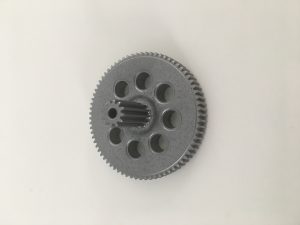
この鉄系焼結金属の加工品は、自動車・二輪業界向けに使用される焼結歯車(ギア・ギヤ)です。
歯車の歯部は成形にて加工・製作を行っており、マシニングセンターでは歯車のボス部へのφ3の穴あけ・リーマ・面取り加工を行っています。歯車外径に対して内径の振れ度が厳しいため、高精度な内径穴あけ加工が要求されています。
小型ギア(歯車)
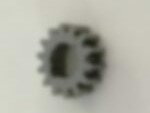
この小型ギア(歯車)は、鉄系の焼結金属にて製作された切削加工品です。端面と内径、外径を平面研磨と円筒研磨にて研磨加工し、旋盤加工でギア(歯車)の厚みを調整しています。また、同軸度は0.025、面相度はRz3.2(Ra0.4)の高い精度を出しています。
アルミダイカスト製 円柱型油圧ポンプケース
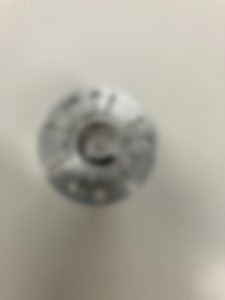
この油圧ポンプのケースは、アルミダイカストから加工を行った機械加工品です。加工方法として内径と外周を旋盤にて加工し、穴あけをマシニングにて加工を行っています。
油圧ポンプは旋盤加工で行う内径・外径の偏心に注意が必要です。専用の特殊治具を社内で内製化し、位置ズレが起こらないように固定してから旋盤加工することで、高い精度の加工を行っています。
アルミダイカスト製 円柱型油圧ポンプケース②
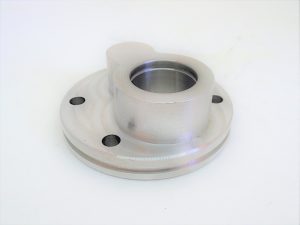
この油圧ポンプのケースは、アルミダイカストから加工を行った試作加工品です。加工方法として内径と外周、外周溝を旋盤にて加工し、穴あけや異形状部分をマシニングにて加工を行っています。
本製品は旋盤加工で行う内径・外径の偏心量が非常に大きく、専用の特殊治具を社内で内製化し、位置ズレが起こらないように固定してから旋盤加工することで、高い精度の加工を行っています。また、異形状部分の加工もCADや3Dデータを御支給頂ければ、同様の加工を対応可能です。
アルミ製 マニホールドブロック
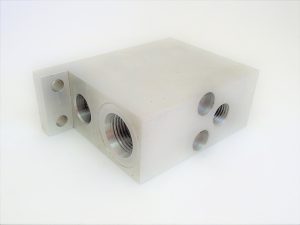
この製品は、アルミソリッド(ブロック)から加工を行った機械加工品です。加工方法としてマシニングにて6面加工を行っております。
段付き穴が非常に高精度な製品となっておりますが、専用の特殊工具を社内で内製化し、同軸度や穴径を確保しながらの加工を行っている製品となっております。
外側12枚フィン 圧粉磁心サンプル
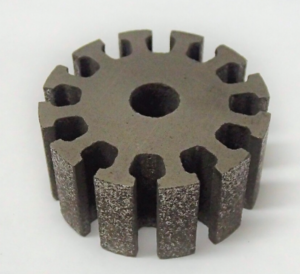
こちらは、外側12枚フィンを持つ圧粉磁心サンプルです。軟磁性材製のΦ30×13Lの小径円柱ブランク材を基材とし、切削加工によって製作された当社オリジナルの開発的な形状です。加工精度として、平行度・直角度を2~8/100に仕上げることで、高い寸法精度と機能性を実現しています。
内側12枚フィン 圧粉磁心サンプル
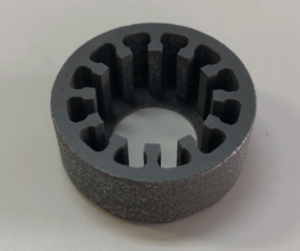
こちらは、内側12枚フィンを持つ圧粉磁心サンプルです。軟磁性材製のΦ30×15Lの小径円柱ブランク材を基材とし、切削加工によって製作された当社オリジナルの開発的な形状です。加工精度として、平行度・直角度を2~8/100に仕上げ、高い寸法精度を確保しています。
9突起 圧粉磁心サンプル
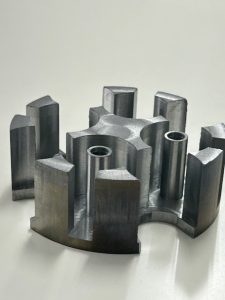
こちらは、圧粉磁心サンプルです。軟磁性材を素材としたΦ110×35Lの大径円柱ブランク材を基材とし、切削加工により製作された当社オリジナルの開発的な形状です。加工精度として、平行度・直角度を2~8/100に仕上げ、高度な寸法精度と機能性を実現しています。
本製品は、突起部9個と2つの穴を精密に加工する設計となっています。軟磁性材は硬度が高い一方で脆く、加工中に先端や角部が欠けやすいという特性があるため、高い加工技術が求められます。特に、全高が高い複雑な形状においては、振動の抑制や刃具の切れ味を維持するための高度な管理が必要です。当社では、自社製の軟磁性材専用切削刃具を使用し、これらの課題をクリアすることで、高難度の加工にも対応しています。
8突起 圧粉磁心サンプル
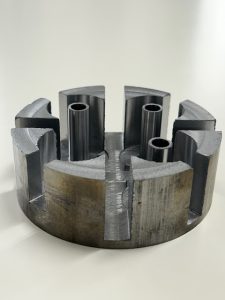
こちらは、圧粉磁心サンプルです。軟磁性材製のΦ110×35Lの大径円柱ブランク材を基材とし、切削加工により製作した当社オリジナルの開発的な形状です。加工精度として、平行度・直角度を2~8/100に仕上げ、高い寸法精度と機能性を実現しています。
本製品は、突起部8個と中心を含む3個の穴を精密加工して仕上げています。この加工には、軟磁性材特有の「硬度が高く脆い」という性質への対応が求められます。特に、全高が高い構造のため、振れを抑えながら刃具の切れ味を維持することが重要です。こうした特性を考慮し、当社では自社開発の軟磁性材専用切削刃具を使用して、他社との差別化を図った高難度加工を実現しています。
12突起 アキシャルギャップモーター用圧粉磁心コア
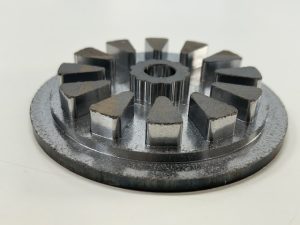
こちらは、アキシャルギャップモーター用の圧粉磁心コアです。軟磁性材製のΦ120×20Lの大径円柱ブランク材を基材とし、切削加工によって製作した当社オリジナルの開発的な形状です。加工精度として、非常に加工難易度が高い軟磁性材ではありますが、平行度・直角度を2~8/100という高精度仕上げを実現しています。
このアキシャルギャップモーターコア形状の製品では、突起部12個と中心の穴1個の精密加工が必要になります。しかし軟磁性材は、硬度が高い一方で脆く、加工中に先端や角部が欠けやすいという特性があります。そのため、振れの抑制や切削刃具の切れ味を適切に維持することが重要です。当社では、自社製の軟磁性材専用切削刃具を開発製造し、軟磁性材加工に使用することで、他社と差別化された高難度加工を実現しています。
焼結金属やMIM成形品など、粉末冶金製品の追加工・量産のご相談は焼結金属加工.COMへ
焼結金属、MIMといった粉末冶金の金属粉末成形技術は、それぞれに特有の製法と強みを持ち、用途や生産規模に応じて最適な工法選定が求められます。しかし、いずれの工法においても、最終的な機能を確保するためには、高精度な追加工(2次加工)が不可欠です。
焼結金属加工.COMでは、成形品に対する穴あけや溝加工、精密研磨などの追加工を試作段階から量産に至るまで、変わらぬ精度で対応できる体制を整えています。さらに、難削材への対応、専用ライン設計、特殊工具の内製化による工程短縮、開発部との連携による設計支援など、他社にはない包括的な技術支援を行っております。
「試作時は問題なかったのに、量産になって精度が出ない」
「追加工ができる外注先が見つからない」
「複雑形状や難削材で他社に断られた」
このような課題をお持ちであれば、ぜひ焼結金属加工.COMへご相談ください。
設計から量産まで、一貫した品質と技術力でお客様の製品開発・生産を強力にサポートいたします。